【摘 要】通過對(duì)一種典型的飲料瓶吹塑模具型腔高速數(shù)控加工工藝的設(shè)計(jì),分析并總結(jié)出模具高速加工的工藝特點(diǎn),進(jìn)一步明確加工方案的合理選擇、加工設(shè)備和刀具的有效利用,切削用量等參數(shù)的最佳設(shè)定及現(xiàn)代制造軟件的靈活應(yīng)用,是保證模具加工質(zhì)量、提高 生產(chǎn)效率的重要途徑,也為類似的模具零件數(shù)控工藝設(shè)計(jì)提供了很好的借鑒。
引言
隨著三維造型軟件的不斷提高,在模具設(shè)計(jì)、制造過程中,異型曲面的設(shè)計(jì)與自由曲面應(yīng)用日趨增加。同時(shí),加工制造過程中對(duì)形狀及尺寸精度的要求越來越高,供貨期限也越來越短,這就對(duì)加工過程有了更高的要求。高速數(shù)控加工技術(shù)對(duì)以往的加工工藝有較大影響,逐步改變了以往的加工工藝流程。高速加工中心可以加工熱處理后的模具鋼,可以有效減少加工過程的時(shí)間,降低加工成本,提高加工生產(chǎn)效率。下面通過實(shí)例對(duì)典型吹塑模具型腔的數(shù)控加工工藝進(jìn)行分析。
1.模具型腔工藝性分析
1.1結(jié)構(gòu)分析
根據(jù)產(chǎn)品造型,設(shè)計(jì)出來的型腔如圖1 所示,型腔面由多個(gè)曲面組成,而且表面粗糙度要求較高。型面中部旋轉(zhuǎn)凸臺(tái)進(jìn)行分度后采用局部區(qū)域加工。
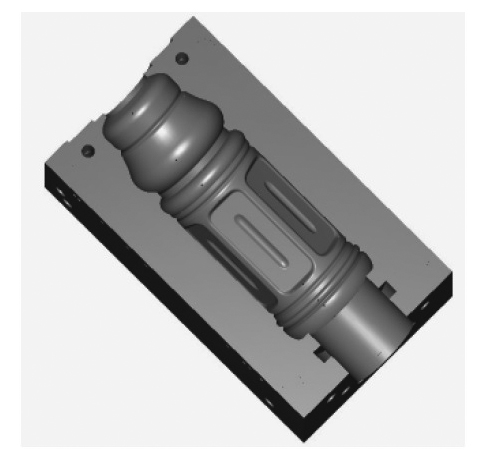
圖1 飲料瓶吹塑模具型腔加工模型
1.2材料分析
型腔材料為鍛造鋁合金,但鋁合金存在剛性強(qiáng)度低、韌性高及延展性強(qiáng)等切削性能特點(diǎn),為保證切削效率,解決剛性強(qiáng)度低問題,因而所用的刀具前角小、比較鋒利,切削轉(zhuǎn)速高、進(jìn)給速度快。但韌性高則會(huì)給高速切削帶來兩個(gè)方面的問題:一是在高速切削狀態(tài)下容易導(dǎo)致黏結(jié)的現(xiàn)象;二是由于鋁材具有高度的延展性,它有可能會(huì)形成條狀紋。因此,加工鋁合金時(shí)應(yīng)考慮以下幾個(gè)方面。
(1)刀具材料及合理幾何參數(shù)選擇。加工鋁合金的刀具材料可選用W8Cr4V高速鋼和YG8、YG6、YG8N 等硬質(zhì)合金,YG6 宜用于余量均勻條件下的連續(xù)加工和半精加工。
(2)切削用量,由于鋁合金的強(qiáng)度和硬度比較低且導(dǎo)熱性好,因此可以獲得較高的進(jìn)給速度,適于進(jìn)行高速加工。
(3)冷卻潤(rùn)滑,用硬質(zhì)合金刀具粗加工鋁合金時(shí),因吃刀量少,進(jìn)給速度高,切削熱主要集中在廢鋁屑上,一般可不用冷卻潤(rùn)滑,而用高壓空氣冷卻將高溫碎屑吹走。
1.3擬定工藝方案
對(duì)復(fù)雜型腔模具制造工藝應(yīng)根據(jù)型腔形狀、尺寸、技術(shù)要求并結(jié)合本單位設(shè)備情況等具體條件來制定。該飲料瓶吹塑模具型腔可考慮以下加工方案進(jìn)行制造。
在高速加工中心,該型腔的銑削加工分四大步:先采用實(shí)體挖槽對(duì)其進(jìn)行粗加工,然后采用曲面銑削進(jìn)行半精加工和精加工,針對(duì)其型面中部旋轉(zhuǎn)凸臺(tái)進(jìn)行分度后采用局部區(qū)域加工,編程坐標(biāo)原點(diǎn)設(shè)在型腔軸線的瓶底處。
2.高速銑削的加工編程
2.1粗加工的高速銑削編程
選用φ20R0.5 銑刀,采用斜線下刀方式,可以改善進(jìn)刀時(shí)的切削狀態(tài),保持較高的進(jìn)刀速度和較低的切削負(fù)荷,其參數(shù)設(shè)置如圖2 所示。
圖2 斜線下刀設(shè)置對(duì)話框
選擇曲面粗加工方法中的cons tan(t 平行環(huán)繞并清角)從外徑內(nèi)走刀方式,銑削方向?yàn)轫樸?,第一刀背吃刀?.5 mm, 刀路重疊50%,參數(shù)設(shè)置如圖3 所示,轉(zhuǎn)速為15 000 r/min, 進(jìn)給速度為 5 000 mm/mim,粗加工和半精加工時(shí)將擬合誤差值,設(shè)為0.5,太小加工速度會(huì)減慢,加工時(shí)間會(huì)變長(zhǎng)。

圖3 刀路重疊設(shè)置對(duì)話框
2.2半精加工的高速銑削編程
由于MasterCAM 沒有半精加工設(shè)置,因此選擇的是曲面精加工的Paraiiel 命令。選用 φ12 mm 球頭銑刀。因粗加工采用 φ20 mm 刀具型腔底面留有較大的余量,為了改善切削狀況,保持較高的速度和較低的切削負(fù)荷,同時(shí)以避免產(chǎn)生縱向刀紋。如果瓶口部分圓弧較小,再添加一把 φ8mm 球刀進(jìn)行加工,以獲得整個(gè)型腔表面精加工的均勻預(yù)留量。最后選用 φ6 mm 球刀半精加工,轉(zhuǎn)速為 24 000r/min,進(jìn)給速度為 3 500 mm/min。在生成加工刀具運(yùn)動(dòng)軌跡時(shí),考慮到加工效率等因素,故應(yīng)選擇往Zigzag 走刀方式,設(shè)置切削間距為 0.35 mm,雙向切削預(yù)留 0.1 mm 余量,切削角度設(shè)置為45°,其參數(shù)設(shè)置如圖4 所示,選軸向?yàn)榍邢鞣较颉?/span>
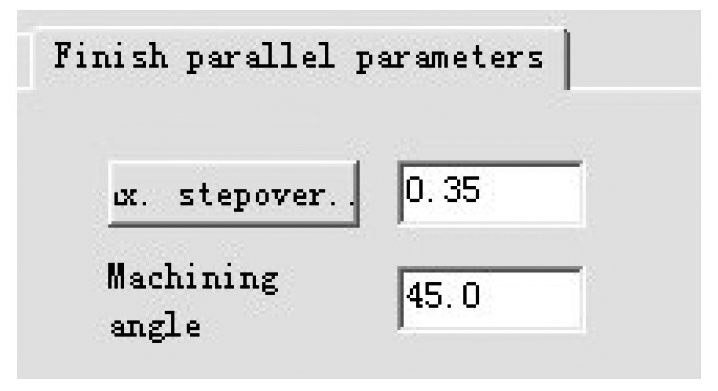
圖4 切削角度設(shè)置對(duì)話框
2.3精加工刀具路徑編程
精加工的刀具路徑軌跡選擇型腔底端圓弧的法線方向?yàn)?切削進(jìn)刀及加工進(jìn)給方向,這樣生成的刀具路徑比較均勻, 以便后期拋光時(shí)不會(huì)有明顯的刀具切削痕跡。為了在加工后 達(dá)到表面粗糙度的要求,盡量采用φ6 mm 的球頭銑刀,并結(jié)合刀具路徑交叉重疊的方法進(jìn)行精加工。目的是半精加工時(shí)刀具切削路徑角度為繞中軸線45°進(jìn)行加工,因此精加工的工序是刀具路徑沿著型腔X軸的徑向進(jìn)行加工,可達(dá)到最 好去除表面凸點(diǎn)的效果。具體參數(shù)設(shè)置為轉(zhuǎn)速24 000 r/min,進(jìn)給速度為2 500 mm/min。一般擬合誤差應(yīng)為加工零件的1/5~ 1/10,而本零件的誤差一般是在0.05 的數(shù)量級(jí),因此數(shù)控編程中的擬合誤差應(yīng)控制在 0.005 左右,必須在精加工自動(dòng)編程中利用圖5 對(duì)話框進(jìn)行擬合誤差的設(shè)置。
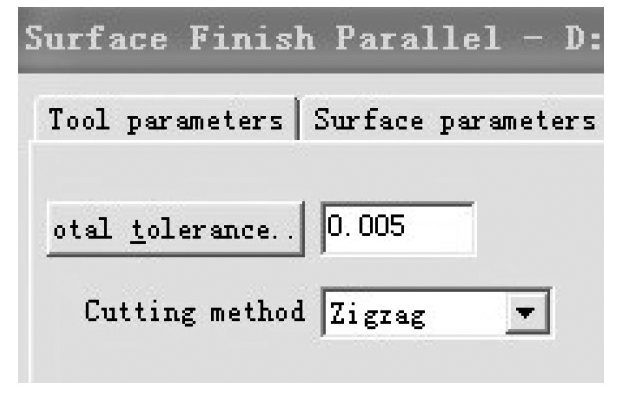
圖5 擬合精度設(shè)置對(duì)話框
2.4精加工的區(qū)域加工編程
由于此型面屬于軸類轉(zhuǎn)軸面,型腔內(nèi)兩側(cè)面矩形凸臺(tái)加工留有欠切,旋轉(zhuǎn)60°后采用區(qū)域加工,加工范圍為矩形凸臺(tái)的四周倒角與角臺(tái)上方的半圓形凸起部分。由于旋轉(zhuǎn)后工件單側(cè)升高了,為了不發(fā)生撞刀而采用了加長(zhǎng)刀具。為了改善表面質(zhì)量及表面刀紋的一致性,4 個(gè)倒角面采用先加工兩個(gè)長(zhǎng)側(cè)面,再加工兩個(gè)端面。這樣可以有效地避免加工到凸臺(tái)時(shí)頻繁抬刀的動(dòng)作,節(jié)約了輔助時(shí)間,提高了效率,具體參數(shù)設(shè)置跟精加工時(shí)一樣,區(qū)域加工刀具路徑如圖6 顯示效果圖。
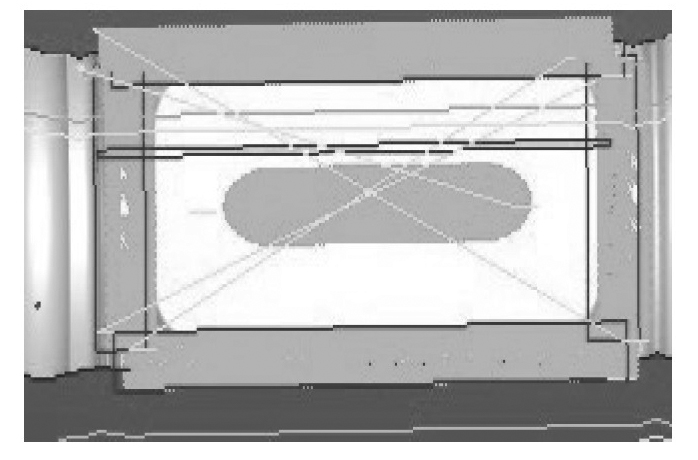
圖6 區(qū)域加工刀路
3.總結(jié)
本文應(yīng)用了MasterCAM 數(shù)控加工編程軟件,結(jié)合典型型腔體進(jìn)行數(shù)控加工程序的編制,結(jié)合有效的高速數(shù)控加工工藝,將其應(yīng)用于實(shí)際生產(chǎn)中,有效提高數(shù)控生產(chǎn)加工效率及加工成品質(zhì)量,盡量縮短裝刀長(zhǎng)度,以減少刀具振動(dòng),延長(zhǎng)刀具壽命,提高加工精度。