孫 晉,胡 法,胡硯磊,武志軍
(中國(guó)石油化工股份有限公司北京化工研究院,北京 100013)
摘要:研究了冷卻速度、擠出速度和拉伸比等不同擠出工藝對(duì)管材物理性能及殘余應(yīng)力的影響,結(jié)果表明,隨著冷卻和擠出速度的增加,PE管材縱向回縮率增大,靜液壓和SCG破壞時(shí)間逐漸降低。通過盲孔應(yīng)變法研究了不同擠出工藝對(duì)管材內(nèi)外層的釋放應(yīng)變和殘余應(yīng)力分布的影響,研究表明,采用理想化的均勻分布模型不適用于殘余應(yīng)力的定量評(píng)價(jià),采用非均勻應(yīng)力分布模型計(jì)算得到的管材外層的殘余應(yīng)力隨著冷卻和擠出速度的增加而增大,而管材內(nèi)層的殘余應(yīng)力變化較小,由于管材沿壁厚方向冷卻速度的不均勻,內(nèi)外層殘余應(yīng)力分布存在差異。最終,通過對(duì)管材內(nèi)中外層分別進(jìn)行拉伸、密度和結(jié)晶度等物理性能試驗(yàn),進(jìn)一步證明了盲孔法定量評(píng)價(jià)殘余應(yīng)力的有效性。同時(shí)試驗(yàn)發(fā)現(xiàn),當(dāng)擠出拉伸比太高時(shí),分子鏈取向嚴(yán)重,管材縱向回縮率增大,靜液壓和耐SCG性能下降,管材外層殘余應(yīng)力的最大值為14.6MPa,與材料拉伸屈服強(qiáng)度相比,提高了50%。
關(guān)鍵詞:擠出工藝;殘余應(yīng)力;盲孔應(yīng)變法;非均勻應(yīng)力分布;分層測(cè)試
0 引言
近年來,隨著聚烯烴材料聚合技術(shù)的不斷創(chuàng)新和大型生產(chǎn)設(shè)備的改進(jìn),塑料管道的應(yīng)用規(guī)格越來越大,其應(yīng)用已經(jīng)從傳統(tǒng)的市政燃?xì)?、供水和建筑領(lǐng)域發(fā)展到工業(yè)領(lǐng)城,例如市政中水輸送、廢水處理和輸送、海水淡化、核工業(yè)等。開發(fā)高強(qiáng)、輕質(zhì)、耐磨、耐沖擊、耐腐蝕的大口徑塑料管道是未來塑料行業(yè)的主要發(fā)展方向之一[1-3]。但是,由不少實(shí)際案例可知,大口徑厚壁管材擠出加工產(chǎn)生的殘余應(yīng)力造成管材開裂,使用壽命縮短,給工程帶來重大隱患。研究管材殘余應(yīng)力的產(chǎn)生原因,并且從理論上分析、計(jì)算殘余應(yīng)力的分布,對(duì)于模具設(shè)計(jì)、工藝優(yōu)化和提高產(chǎn)品質(zhì)量均具有重要的意義[4]。
殘余應(yīng)力是衡量產(chǎn)品質(zhì)量的重要指標(biāo)之一,對(duì)產(chǎn)品的疲勞強(qiáng)度、抗脆斷能力、抗應(yīng)力腐蝕開裂及高溫蠕變開裂能力和使用壽命等均具有十分重要的影響。許多結(jié)構(gòu)或零件的損壞并不是由外加載荷引起的,而是由存在不合理的殘余應(yīng)力造成的。殘余應(yīng)力測(cè)試方法可分為2類,分別為非破壞性無損傷的物理測(cè)量法及具有一定損傷性的機(jī)械釋放測(cè)量法[5-6]。物理測(cè)量法對(duì)樣品表面要求較高,設(shè)備較復(fù)雜、價(jià)格昂貴。目前,盲孔法已成為應(yīng)用最廣泛的機(jī)械釋放測(cè)量法之一,主要用于測(cè)量機(jī)械零部件和構(gòu)件制造工藝過程中產(chǎn)生的殘余應(yīng)力[7-10]。殘余應(yīng)力測(cè)試方法的研究主要集中在金屬材料和少量工程塑料領(lǐng)域,而聚烯烴高分子材料的殘余應(yīng)力測(cè)試方法的研究較少。文章通過系統(tǒng)地研究不同擠出工藝對(duì)聚乙烯管材物理性能和殘余應(yīng)力的影響,建立一種聚乙烯管材殘余應(yīng)力分布的定性和定量評(píng)價(jià)方法。
1 實(shí)驗(yàn)部分
1.1 主要原料
高密度聚乙烯(HDPE )管材料 :PE100級(jí),黑色,其物理性能如表1所示,市購(gòu)。
1.2 主要儀器及設(shè)備
管材螺桿擠出機(jī):BBC1-90-30,Battenfeld-cincinnati公司;
盲孔法殘余應(yīng)力測(cè)試儀:MTS3000,意大利SINT公司;
管材液壓試驗(yàn)機(jī):1676,德國(guó)IPT公司;
耐慢速裂紋增長(zhǎng)制樣機(jī):德國(guó)IPT公司;
萬能材料試驗(yàn)機(jī):Instron4466,美國(guó)Instron公司;
高低溫試驗(yàn)箱:ZM-10KA,廣州愛斯佩克公司;
密度梯度儀:BHM-2,北京化工研究院;
電子天平:AL104,梅特勒;
X射線衍射儀:X'Pert MPD,PHILIPS公司。
1.3 樣品的制備
為了得到不同殘余應(yīng)力的管材樣品(dn250,SDR11),按照熔體和冷卻水的溫度差值以及擠出速度,設(shè)計(jì)了管材在不同冷卻和擠出速度下的工藝參數(shù)(A~D),如表2所示。其中,與工藝A和B相比,工藝C冷卻速度最小,并且擠出速度最慢,工藝條件相對(duì)優(yōu)化。同時(shí)工藝A、B、C采用常規(guī)的dn250口模和dn250芯模,擠出拉伸比為1.43。工藝D采用特殊的dn250口模和dn200芯模,擠出拉伸比增加至2.23,進(jìn)一步提高了樣品的殘余應(yīng)力水平。
1.4 性能測(cè)試與結(jié)構(gòu)表征
縱向回縮率測(cè)試:按照GB/T6671—2001進(jìn)行測(cè)試,測(cè)試溫度為110℃,樣品放置4h后冷卻至室溫,計(jì)算3個(gè)平行試樣的算術(shù)平均值。
斷裂伸長(zhǎng)率測(cè)試:管材專用料斷裂伸長(zhǎng)率按照GB/T1040.2—2006進(jìn)行測(cè)試,樣品類型1B;管材樣品斷裂伸長(zhǎng)率按照GB/T8804. 3—2003進(jìn)行,樣品類型I;拉伸速率均為50mm/min,計(jì)算5個(gè)平行試樣的算術(shù)平均值。
靜液壓強(qiáng)度測(cè)試:按照 GB/T6111 —2003 進(jìn)行,采用A型封頭,試驗(yàn)溫度為20℃,環(huán)應(yīng)力分別為12.4 和13.5MPa,記錄管材在恒壓下的破壞時(shí)間。
SCG性能測(cè)試:按照GB/T 18476—2001進(jìn)行,試驗(yàn)溫度80℃ ,試驗(yàn)壓力0.92MPa,記錄管材在恒壓下的破壞時(shí)間。
管材分層拉伸測(cè)試:為了進(jìn)一步分析管材沿壁厚方向外、中和內(nèi)層的性能差異,按照GB/T 8804.3—2003采用機(jī)械加工方法沿壁厚方向平均銑削為3層,制取啞鈴型試樣(類型1)。試驗(yàn)分別測(cè)量管材外、中和內(nèi)層的拉伸性能,拉伸速率為50mm/min。
密度測(cè)試:采用密度梯度法,按照 GB/T 1033.2—2010進(jìn)行試驗(yàn)。
結(jié)晶度測(cè)試:采用 PHILIPS公司X射線衍射儀進(jìn) 行結(jié)晶度分析。掃描速度為0. 02°/s,掃描范圍為15°~30°。采用衍射峰的積分面積來計(jì)算試樣的結(jié)晶度,如式(1) 所示。
結(jié)晶度=晶相積分面積/( 晶相積分面積+非晶相積分面積) × 100%
(1)
管材殘余應(yīng)力測(cè)試:按照 ASTM E837—2013a 鉆孔法分別測(cè)量管材內(nèi)外層沿壁厚方向上的殘余應(yīng)力分布[11]。為了避免鉆孔在測(cè)量區(qū)域產(chǎn)生熱量,鉆頭轉(zhuǎn)速很低(250r/min) ,進(jìn)給速度很緩慢(0. 2 mm/min) ,最大程度地減少對(duì)殘余應(yīng)力的影響。在鉆孔過程中,記錄得到管材3個(gè)方向上的釋放應(yīng)變隨著鉆孔深度的變化曲線,最終,計(jì)算得到管材內(nèi)外層的Von Mises 等效殘余應(yīng)力σvon 。
2 結(jié)果與討論
2. 1 不同工藝對(duì)管材物理性能的影響
不同工藝擠出管材的縱向回縮率、靜液壓性能和耐慢速裂紋增長(zhǎng)SCG等物理性能測(cè)試結(jié)果如表3所示。由管材縱向回縮率可知,在熱歷史影響下,管材沿縱向尺寸變化的穩(wěn)定性側(cè)面反映了管材加工冷卻過程產(chǎn)生的殘余應(yīng)力值。由于取向的高分子鏈占據(jù)較大的自由體積,處于較高的能態(tài),仍有向低能態(tài)發(fā)展的趨勢(shì)(如松弛、卷曲、纏繞或重結(jié)晶等),在二次加熱過程中發(fā)生尺寸收縮,取向程度降低。因此,可采用縱向尺寸回縮率初步衡量管材殘余應(yīng)力水平,即縱向尺寸回縮率越高,殘余應(yīng)力水平越高。通過比較工藝 A、B和C可知,工藝A的冷卻速度和擠出速度最大,縱向尺寸變化率最大(縱向回縮率 1.2%),其殘余應(yīng)力水平最高;而工藝C冷卻速度和擠出速度較低,縱向回縮率較低(0.82%),因此,殘余應(yīng)力水平較低。同時(shí),工藝D的縱向回縮率最大,其值為1.6%。這是由于,拉伸比最高,PE分子鏈取向程度最大,殘余應(yīng)力水平提高。因此,采用縱向回縮率可以初步判斷管材殘余應(yīng)力水平,但是,即使是工藝不合理的A和D,其縱向尺寸回縮率仍滿足產(chǎn)品標(biāo)準(zhǔn)GB/T13663. 2—2018的要求(≤3%) ,因此,其僅能作為定性的比較方法。
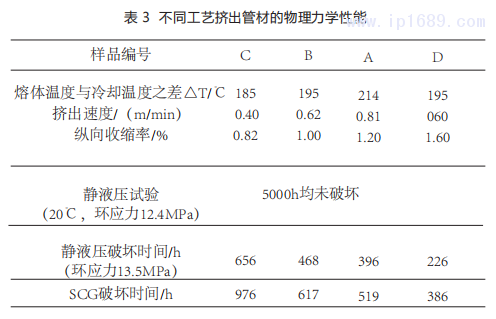
按照 GB/T 13663. 2—2018標(biāo)準(zhǔn)要求(20℃、環(huán)應(yīng)力12. 4MPa) 進(jìn)行管材靜液壓試驗(yàn),不同工藝擠出管材的物理力學(xué)性能如表3所示。 由表3可知,4種管材在恒壓5000h后均未發(fā)生破壞。因此,常規(guī)條件的靜液壓試驗(yàn)難以衡量不同工藝對(duì)管材靜液壓性能的影響。將環(huán)應(yīng)力增加至13.5MPa后,所有管材均在1000h以內(nèi)發(fā)生韌性破壞。因此,隨著冷卻和擠出速度的增加( C-B-A),PE管材的靜液壓破壞時(shí)間逐漸降低,這表明,擠出冷卻過程中產(chǎn)生的殘余應(yīng)力差異對(duì)于管材耐靜液壓性能的影響。而由于工藝D的拉伸比太大,聚乙烯分子鏈沿管材軸向上取向嚴(yán)重,管材環(huán)向承壓能力降低,其靜液壓破壞時(shí)間最短。
慢速裂紋增長(zhǎng)導(dǎo)致的破壞屬于典型的脆性破壞,PE材料在低應(yīng)力下,晶區(qū)間的系帶分子鏈發(fā)生解纏結(jié)和松弛[12-14]。而系帶分子鏈的解纏速度主要受其纏結(jié)密度、分子量及分布和晶體結(jié)構(gòu)等參數(shù)的影響。對(duì)于同一種管材料而言,不同工藝影響了材料的結(jié)晶和取向行為,導(dǎo)致其結(jié)晶度降低或結(jié)晶不完善,系帶分子鏈纏結(jié)密度降低,管材耐SCG性能逐漸下降。由表3 可知,隨著冷卻和擠出速度的增加(C-B-A),PE管材的SCG破壞時(shí)間逐漸縮短。工藝A冷卻和擠出速度較快,其結(jié)晶較不完善,由此所引起的殘余應(yīng)力也較大,系帶分子鏈的解纏結(jié)速度較快,導(dǎo)致工藝A下管材的SCG破壞時(shí)間最短。證明了冷卻和擠出速度對(duì)于管材殘余應(yīng)力的影響。同時(shí)由于較大的拉伸比所導(dǎo)致的取向,工藝D管材SCG破壞時(shí)間逐漸降低。
2. 2 不同工藝對(duì)管材殘余應(yīng)力的影響
文章采用盲孔應(yīng)變法分別測(cè)量不同工藝( A ~ D) 擠出管材內(nèi)外層沿壁厚方向上的殘余應(yīng)力分布。在鉆孔過程中,在鉆孔周圍的殘余應(yīng)力得到釋放,該過程中產(chǎn)生的微應(yīng)變被粘貼在試樣上的應(yīng)變計(jì)記錄下來,得到管材3個(gè)方向上的釋放應(yīng)變與鉆孔深度的關(guān)系曲線。應(yīng)變計(jì)粘貼的位置和方向如圖1所示。從圖 1 中可以看出,第一方向?yàn)檠毓懿臄D出的軸向方向,第二方向與管材軸向成45°夾角,第三方向?yàn)榕c管材軸向成90℃夾角的環(huán)向方向。最終,計(jì)算得到管材內(nèi)外層的最大主應(yīng)力σmax、最小主應(yīng)力σmin、最大主應(yīng)力角度β和Von Mises 等效殘余應(yīng)力σvon等。最大主應(yīng)力角度β為最大主應(yīng)力和應(yīng)變計(jì)第一方向的順時(shí)針夾角。圖2~4 為管材內(nèi)外層在3個(gè)方向上的釋放應(yīng)變與鉆孔深度的關(guān)系。由圖2可知,在第一方向(軸向) 上,管材外層的釋放應(yīng)變均隨著鉆孔深度的增加逐漸變大。
圖 1 應(yīng)變計(jì)的類型( a) 和粘貼位置( b )
圖 2 管材內(nèi)外層的釋放應(yīng)變與鉆孔深度的關(guān)系( 第一方向)
而管材內(nèi)層的釋放應(yīng)變相對(duì)較小,并且變化趨勢(shì)較小。由圖3可知,在第二方向(與軸向呈 45°角)上,不同工藝管材內(nèi)外層的釋放應(yīng)變變化趨勢(shì)與第一方向類似,管材外層釋放應(yīng)變逐漸增大,但是,管材內(nèi)層的釋放應(yīng)變相對(duì)較小。由圖4可知,在第三方向(環(huán)向),不同工藝( A、B和C) 管材內(nèi)外層的釋放應(yīng)變值與第一方向相比均較小,但是,工藝D管材的釋放應(yīng)變隨著鉆孔深度的變化相對(duì)較大。這是由于,擠出拉伸比太大,環(huán)向上的殘余應(yīng)力較大。
圖 3 管材內(nèi)外層的釋放應(yīng)變與鉆孔深度的關(guān)系( 第二方向)
圖 4 管材內(nèi)外層的釋放應(yīng)變與鉆孔深度的關(guān)系( 第三方向)
按照 ASTM E837 方法和理想化的應(yīng)力均勻分布模型計(jì)算得到管材內(nèi)外層的最大主應(yīng)力σmax、最小主應(yīng)力σmin、最大主應(yīng)力角度β和Von Mises 等效殘余應(yīng)力σvon,如表4所示。應(yīng)變計(jì)第一方向?yàn)檠毓懿妮S向,因此,管材內(nèi)層最大主應(yīng)力方向是以軸向?yàn)橹鳎@表明,內(nèi)層殘余應(yīng)力主要是由分子鏈沿?cái)D出方向取向。而管材外層最大主應(yīng)力方向是以環(huán)向?yàn)橹?,這表明,外層殘余應(yīng)力主要是由冷卻不均勻。但是,不同工藝擠出管材內(nèi)外層殘余應(yīng)力均約為 1~3MPa,并且差異較小,這與實(shí)際情況不一致。因此,理想化的均勻分布模型不適用于PE管材殘余應(yīng)力的測(cè)量。
按照 ASTM E837 方法和理想化的應(yīng)力均勻分布模型計(jì)算得到管材內(nèi)外層的最大主應(yīng)力σmax、最小主應(yīng)力σmin、最大主應(yīng)力角度β和Von Mises 等效殘余應(yīng)力σvon,如表4所示。應(yīng)變計(jì)第一方向?yàn)檠毓懿妮S向,因此,管材內(nèi)層最大主應(yīng)力方向是以軸向?yàn)橹?,這表明,內(nèi)層殘余應(yīng)力主要是由分子鏈沿?cái)D出方向取向。而管材外層最大主應(yīng)力方向是以環(huán)向?yàn)橹鳎@表明,外層殘余應(yīng)力主要是由冷卻不均勻。但是,不同工藝擠出管材內(nèi)外層殘余應(yīng)力均約為 1~3MPa,并且差異較小,這與實(shí)際情況不一致。因此,理想化的均勻分布模型不適用于PE管材殘余應(yīng)力的測(cè)量。
2. 3 管材分層試驗(yàn)驗(yàn)證
將管材樣品按照壁厚方向平均銑削為3層,分別進(jìn)行拉伸、密度和結(jié)晶度等試驗(yàn),其測(cè)試結(jié)果如表5所示。從表5中可以看出,管材各層(內(nèi)外中)的斷裂伸長(zhǎng)率差異較小,但是,中間層的拉伸屈服強(qiáng)度、密度和 結(jié)晶度最高,內(nèi)層其次,外層最低。這是由于,管材外層的冷卻速度較快,結(jié)晶相對(duì)不完善,相應(yīng)的拉伸屈服強(qiáng)度、結(jié)晶度和密度逐漸降低。這與采用盲孔法測(cè)量PE管材外層殘余應(yīng)力大于內(nèi)層殘余應(yīng)力的結(jié)果一致,證明了盲孔法定量評(píng)價(jià)殘余應(yīng)力的有效性。
圖 5 管材內(nèi)外層沿鉆孔深度方向上的殘余應(yīng)力分布曲線(非均勻分布模型)
3 結(jié)論
(1)通過研究不同擠出工藝對(duì)管材物理性能的影響,分析了不同管材殘余應(yīng)力的差異。通過試驗(yàn)發(fā)現(xiàn),隨著冷卻和擠出速度的增加,管材縱向回縮率逐漸增大,靜液壓強(qiáng)度和SCG破壞時(shí)間逐漸降低。同時(shí)隨著擠出拉伸比的增大,PE分子鏈冷卻取向程度增大,導(dǎo)致管材的縱向回縮率增加,靜液壓和耐SCG性能下降。
(2)采用盲孔應(yīng)變法對(duì)不同工藝管材樣品內(nèi)外層進(jìn)行了殘余應(yīng)力的定量評(píng)價(jià),結(jié)果表明,采用理想化均勻分布模型計(jì)算得到所有樣品的殘余應(yīng)力分布差異較小,不適用于PE管材殘余應(yīng)力的定量測(cè)試。采用非均勻應(yīng)力分布模型計(jì)算得到管材外層的殘余應(yīng)力隨著冷卻和擠出速度的增加而增大,而管材內(nèi)層的殘余應(yīng) 力變化較小(<4MPa)。這是由于,管材內(nèi)外層冷卻速度的不均勻分布?xì)堄鄳?yīng)力分布產(chǎn)生差異。
(3)采用分層評(píng)價(jià)法對(duì)聚乙烯管材的外層、中間層和內(nèi)層樣品分別進(jìn)行拉伸、密度和結(jié)晶度等試驗(yàn),結(jié)果表明,管材外層的拉伸屈服強(qiáng)度、密度和結(jié)晶度最低。這與殘余應(yīng)力的定量評(píng)價(jià)結(jié)果一致,進(jìn)一步證明了盲孔法定量評(píng)價(jià)殘余應(yīng)力的有效性。
參考文獻(xiàn):
[1] 王占杰,趙艷,郭晶.中國(guó)塑料管道行業(yè)“十二·五”期間發(fā)展?fàn)顩r及“十三·五”期間發(fā)展建議[ J] .中國(guó)塑料,2016,30( 5 ):1-7.
[2] 劉斌,崔志杰.大直徑塑料管道成型牽引裝置開發(fā)進(jìn)展[J] .塑料,2018,47 (3):113-117.
[3] 王登勇,張玉川.大直徑塑料壓力管發(fā)展探析[J] .國(guó)外塑料,2011 ,29 (4 ):38-43.
[4] BEECH S H ,BURLEY C ,BUNN H C.Residual stress in large diameter MDPE water pipe [C] .Plastics Pipes VII ,University of Bath PRI London 1988.
[5] HAUK V.Structural and residual stress analysis by nondestructive methods[M] .Amsterdam:Lausanne,New York:Elsevier,1997.
[6] 劉金娜,徐濱士,王海斗,等.材料殘余應(yīng)力測(cè)定方法的發(fā)展趨勢(shì)[J] .理化檢驗(yàn)( 物理分冊(cè)) ,2013 ,49 ( 10 ):677-682.
[7] CHOI S,BROUTMAN L J.Residual stresses in plastic pipes and fittings I.methods for experimental analysis[ J ] .Polymer( Korea) , 1997,21 (1):71-82.
[8] BEGHINI M ,BERTINI L.Recent advances in the hole drilling method for residual stress measurement [J] .Journal of Materials Engineering and Performance,1998,7 (2):163-172.
[9] MAXWELL A S,TURNBULL A.Measurement of residual stress in engineering plastics using the hole?drilling technique [J] .Polymer Testing,2003 ,22 ( 2 ):231-233.
[10] JANP,JAROSLAV K,PAVEL H,et al.Residual stress distribution in extruded polypropylene pipes [J] .Polymer Testing,2014,40:88-98.
[11] ASTM Committee. Standard test method for determining residual stresses by the hole-drilling strain?gage method:ASTM E837-2013a [S] .West Conshohocken:ASTM International,2013.
[12] NIE M,WANG Q,BAI S B.The effect of cooling mode on slow crack growth resistance of polyethylene pipe [J] .Journal of Macromolecular Science,Part B:Physics,2010,49:640 -651.
[13] BROWN N.Intrinsic lifetime of polyethylene pipelines[ J] .Polymer Engineering & Science,2007,47(4):477-480.
[14] HAMOUDA H B H,SIMOES?BETBEDER M,GRILLON F,et al.Creep damage mechanisms in polyethylene gas pipes[J] .Polymer, 2001 ,42:5425-5437.
[15] 孫晉,華曄,者東梅.?dāng)D出工藝對(duì)聚乙烯管材殘余應(yīng)力分布的影響[J] .中國(guó)塑料,2019,33 (5):56-60.
[16] JANP ,PAVEL H ,JAROSLAV K ,et al. Residual stress in polyethylene pipes[J].Polymer Testing,2016,54:288-295